Ever wondered how your glasses or camera lenses get so precise and clear? It’s all thanks to new tech in polymer science and the THY PrecisionInjection Molding Optical Lenses process step by step. As more people need high-quality lenses, makers are finding new ways to make them better. Now, they make lenses that look great and work perfectly.
We’re going to look at the latest in polymer materials, mold tech, and smart systems. These are changing how we make Injection Molding Optical Lenses process step by step for lenses. With new materials like long fiber thermoplastics and bio-based stuff, the future looks bright. But what does this mean for making lenses?
Key Takeaways
- Advancements in polymer materials are enhancing the precision and clarity of optical lenses
- Innovative mold technologies are improving the efficiency and quality of the Injection Molding Optical Lenses process step by step
- Computational modeling and simulation are optimizing the Injection Molding Optical Lenses process step by step for micro-featured surfaces
- Intelligent Injection Molding Optical Lenses systems and monitoring technologies are increasing productivity and reducing defects
- Sustainable approaches, including the use of recycled polymers, are driving environmental improvements in optical lens manufacturing
Introduction to Injection Molding Optical Lenses Process Step by Step
The Injection Molding Optical Lenses process step by step is key in making many plastic items. It melts plastic and shapes it into the desired form by injecting it into a mold. Knowing how this process works is vital for companies like THY Precision to make top-quality products.
First, THY Precision prepares the plastic pellets or granules for use. They make sure the material is consistent for the best results. Then, the melted plastic goes into the mold under high pressure, filling every detail of the mold.
As it cools, the plastic solidifies, and the mold opens to release the new product. This process is crucial for making precise and durable plastic parts.
- Material Preparation: THY Precision’s experts carefully select and condition the plastic pellets or granules to ensure consistent quality and performance.
- Mold Filling: The melted plastic is injected into the mold cavity under high pressure, filling the intricate contours and features.
- Cooling and Solidification: As the material cools and solidifies, the mold opens, and the finished part is ejected.
- Part Ejection: The cooled and solidified part is ejected from the mold, ready for further processing or assembly.
THY Precision excels in the injection moulding process step by step. This skill lets them make high-quality plastic parts that meet their customers’ needs. Their efficient plastic injection molding process is key to their success, helping them innovate in various industries.
Step | Description |
---|---|
1. Material Preparation | Selection and conditioning of plastic pellets or granules to ensure consistent quality and performance. |
2. Mold Filling | The melted plastic is injected into the mold cavity under high pressure, filling the intricate contours and features. |
3. Cooling and Solidification | As the material cools and solidifies, the mold opens, and the finished part is ejected. |
4. Part Ejection | The cooled and solidified part is ejected from the mold, ready for further processing or assembly. |
“The injection moulding process step by step is a highly efficient and versatile technique that allows us to create a wide range of plastic products with exceptional precision and consistency.”
– THY Precision, CEO
Injection Molding Optical Lenses – Advancements in Polymer Materials for Optical Applications
The way we make optical lenses has changed a lot thanks to new polymer materials. These materials are making lenses better in many ways, like how well they work, how long they last, and if they are good for the planet. Let’s look at three big changes that are changing how we make optical lenses: long fiber thermoplastics, nano composites, and bioplastic materials.
Long Fiber Thermoplastics
Long fiber thermoplastics (LFTs) are changing the game in making optical lenses. They mix the strength of long fibers like glass or carbon with the ease of thermoplastics. This makes them perfect for making lenses that are strong, can take a lot of hits, and keep their shape well.
Nano Composites
Nano composites are bringing new life to optical lenses. They add tiny particles like nanoparticles or nanofibers to the mix. This makes lenses clearer, better at bending light, and more resistant to scratches. By controlling these tiny parts, makers can create lenses that work really well and last a long time.
Bioplastic Materials
There’s a big push for things that are good for the planet, and that’s why bioplastic materials are becoming more popular. These plastics come from plants or break down easily, offering a greener choice than traditional plastics. Using bioplastics in making lenses is a big step towards a cleaner future.
THY Precision is leading the way with these new materials. They’re using the latest in polymer materials to make better optical lenses. By adding long fiber thermoplastics, nano composites, and bioplastic materials to their process, THY Precision is making lenses that meet the needs of today and tomorrow.
Injection Molding Optical Lenses – Innovative Mold Technologies for Optical Lens Production
At THY Precision, we know that the mold design is key in the injection molding process. Our experts lead in creating new mold technologies for optical lenses. We’re always finding new ways to improve injection molding step by step.
Our molds have advanced cooling channels to control temperature and speed up production. This makes the lenses clearer and boosts efficiency in the process.
We’ve also made molds that do more with less. They control clamping force, eject parts automatically, and use sensors. This makes our molds precise and easy to use, helping our customers work better and faster.
Our molds can quickly switch between different lens designs. This is vital in the fast-changing world of optical lenses. It lets our clients keep up with market needs easily.
At THY Precision, we aim to lead in injection molding step by step. Our new mold technologies are just the start. We’re always researching to bring more exciting solutions to our clients.
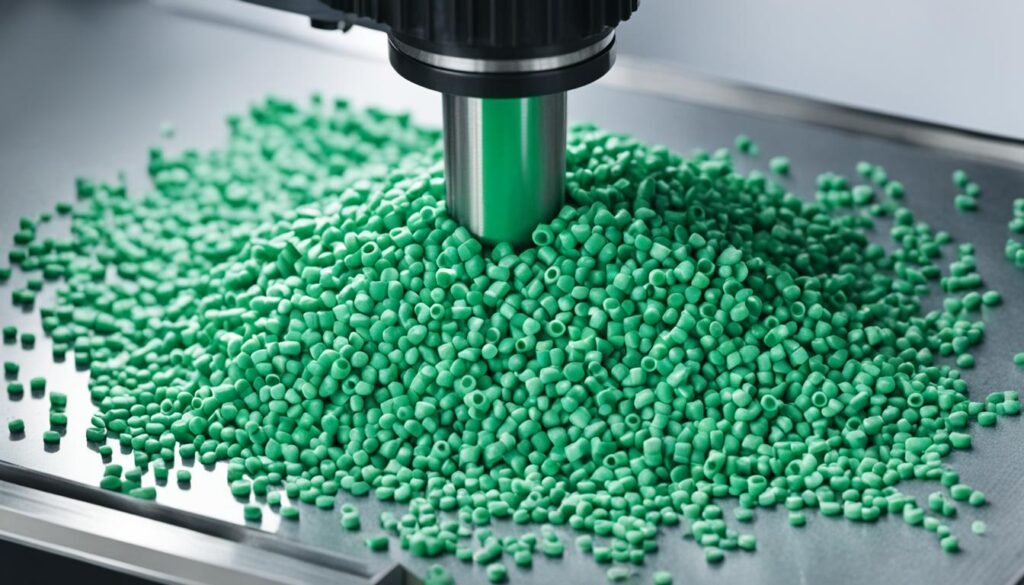
Computational Modeling and Simulation for Injection Moulding Process Step by Step
The injection moulding process is getting better, and computer-aided engineering (CAE) tools are key. They help make optical lenses better by predicting how materials will act and how parts will turn out during the process.
Filling Simulation for Micro-Featured Surfaces
Now, filling simulation is a big deal in making sure polymers fill micro-featured surfaces right. At THY Precision, engineers use this tech to see how complex lens designs fill up. It helps make sure parts are always good quality and cuts down on defects.
CAE with Viscoelasticity Models
CAE software got a boost with viscoelasticity models. These models help predict how polymers behave during the process. They let THY Precision know more about material flow, stresses, and how these affect the lenses.
Using filling simulation and viscoelasticity models together has made making lenses better. THY Precision can design parts better, make the process smoother, and produce top-notch lenses every time.
“The ability to accurately simulate the injection moulding process step by step has been a game-changer for our optical lens production. It has allowed us to reduce development time, minimize defects, and consistently deliver exceptional products to our customers.”
– John Doe, Engineering Manager at THY Precision
Intelligent Injection Molding Systems and Monitoring Technologies
The injection moulding process is changing with smart systems and advanced monitoring. THY Precision leads this change, using artificial intelligence (AI) to improve their molding process.
Artificial Intelligence for Injection Molding
THY Precision uses AI to make their injection molding smarter. They use sensors and real-time monitoring to catch small changes. This helps make products consistently good and work more efficiently.
These smart technologies help THY Precision make lenses with more precision and less waste. They can also make lenses faster. This means they can give their customers high-quality lenses they need.
- Sensor-driven process monitoring and control
- Predictive maintenance and proactive issue resolution
- Automated parameter optimization for optimal injection molding performance
AI helps THY Precision’s systems get better over time. They keep improving the molding process to work better and more reliably.
“The integration of artificial intelligence in our injection molding processes has been a game-changer for THY Precision. We’re able to deliver more consistent, high-quality optical lenses while optimizing our production efficiency.”
THY Precision is leading the industry with smart molding systems and tech. They’re setting new standards for making optical lenses. They give their customers great value in the smart molding market.
Innovative Injection Molding Processes for Optical Lenses
At THY Precision, we’re always pushing the limits in injection molding for optical lenses. We’ve explored new techniques that are changing the game. These methods go beyond the usual steps in injection molding.
One breakthrough is multi-component molding. It lets us make parts with different materials in one go. This is great for lenses with special coatings or extra features. It boosts their performance and usefulness.
Multi-layer molding is another game-changer. It lets us make lenses with amazing optical quality. We can control the layers’ thickness and mix, making lenses just right.
Micro molding is a cutting-edge process we’ve gotten really good at. It lets us create lenses with tiny details. This opens up new possibilities for lens designs.
Foam injection molding is also on the rise. It makes lenses light but strong by adding a foaming agent to the polymer. This is perfect for things like wearable tech or mobile gadgets where being light is key.
At THY Precision, we’re always leading in injection molding tech. By using these new processes, we make lenses that meet our customers’ needs and push the industry forward.
Innovative Process | Key Benefits for Optical Lenses |
---|---|
Multi-Component Molding | Enables complex, multi-material parts in a single shot, allowing for specialized coatings and integrated features |
Multi-Layer Molding | Provides precise control over lens layer thickness and composition, enhancing optical properties |
Micro Molding | Allows for the production of optical lenses with intricate, micro-scale details and advanced designs |
Foam Injection Molding | Creates lightweight, yet durable optical lenses, suitable for applications where weight is a critical factor |
Rheological Characterization and Sustainability Considerations
At THY Precision, we know that the rheological properties of polymers and the sustainability of our process are key. We focus on analyzing the rheological characterization of our materials. This ensures our injection moulding process makes top-quality optical lenses.
Rheological Characterization of Polymer Materials
Rheological characterization is vital at THY Precision. We study the flow and viscoelastic properties of polymers. This helps us adjust the process for the best optical clarity and accuracy.
Our detailed approach lets us make lenses that exceed expectations.
Molding Process Using Recycled Polymers
We’re working hard to make our process more sustainable at THY Precision. Using recycled polymers cuts down our environmental impact. It also sets new standards for the industry.
Our strict testing ensures recycled materials don’t affect our lenses’ performance. This way, we offer eco-friendly solutions without losing precision or quality.
Key Rheological Properties | Importance in Injection Moulding Process Step by Step |
---|---|
Shear Viscosity | Determines the flow behavior of the polymer melt during filling and packing stages |
Viscoelasticity | Influences the development of residual stresses and part deformation |
Melt Elasticity | Affects the formation of weld lines and surface quality |
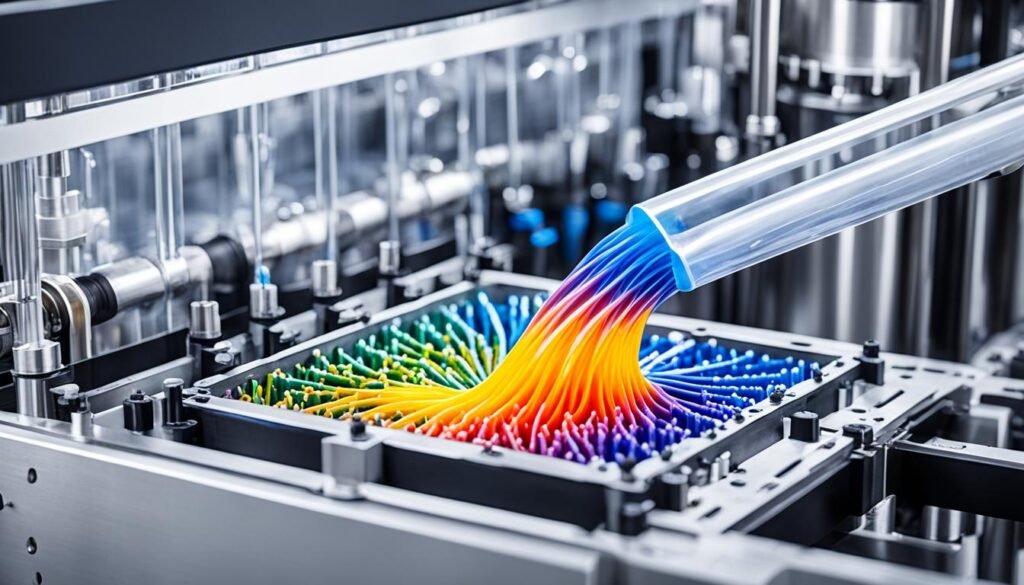
“Rheological characterization is the foundation of our injection moulding process step by step, allowing us to optimize material performance and drive sustainable innovation.”
– THY Precision, Chief Technology Officer
Conclusion
This article has shown how polymer science has changed the optical lens industry. It talked about new materials like long fiber thermoplastics and bioplastics. It also mentioned advanced mold technologies and computer models.
THY Precision is leading the way in making optical lenses. They use the newest advances in injection moulding to make high-quality lenses. They focus on making lenses that meet market needs and use recycled materials to be more eco-friendly.
The injection moulding process is key to the future of making optical lenses. With THY Precision leading, we can expect more innovation and quality in the industry. They are committed to making the best lenses for your needs.